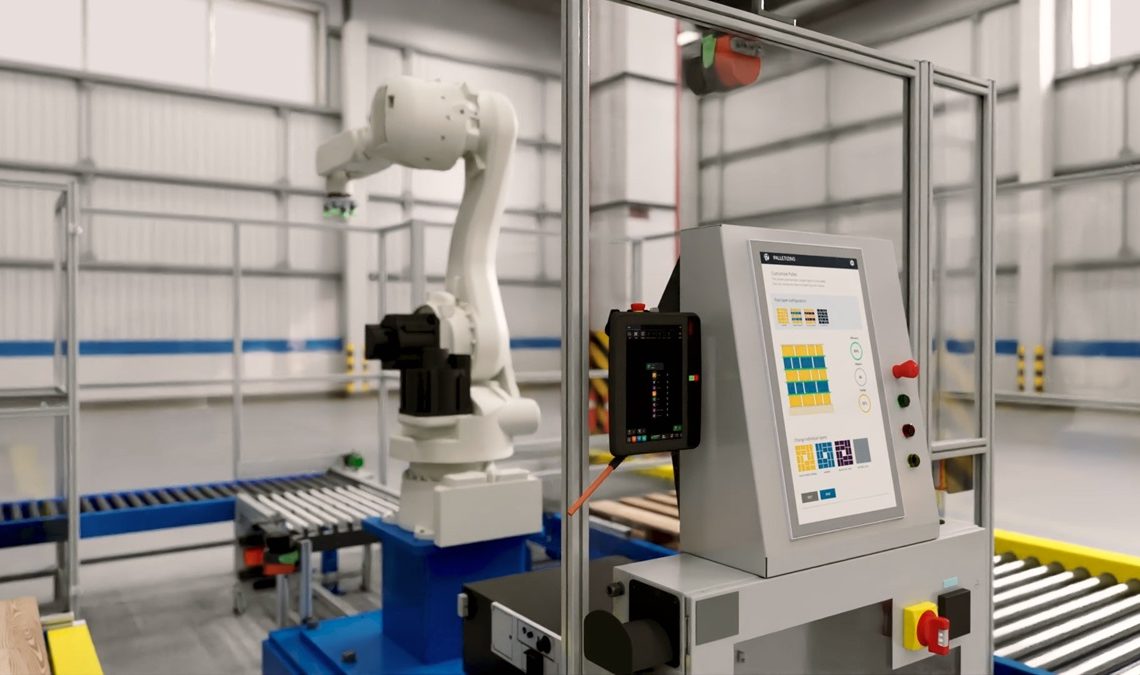
Toyota partnered with Ready Robotics to simulate and program industrial robotics using Nvidia’s Omniverse platform.
The “sim-to-real” robotic programming aims to advance industrial robotics, using both Ready Robotics’ Ready ForgeOS and Nvidia Isaac Sim on the Omniverse platform. Toyota will use the tech for its aluminum hot forging production lines.
The tech is the latest expression of digital twins, where a company simulates a factory in a virtual space, perfects the design, and then builds the factory. The factory, augmented with sensors, sends data back to the digital twin so that the design can be improved based on real-world data. Nvidia’s Omniverse is a platform for digital twins and it’s akin to a metaverse for engineers.
The collaboration is designed to elevate safety and efficiency in Toyota’s manufacturing processes. Traditionally, programming robotic systems for forging involves working with hot metal parts, posing significant safety challenges. The integration of ForgeOS and Nvidia Isaac Sim enables seamless programming in a simulated environment, eliminating risks associated with hot parts.
Ready Robotics simplifies the programming process for robotic systems with ForgeOS, offering time-saving automation solutions. The integration of ForgeOS with Nvidia Isaac Sim ensures best-in-class visual and physics-simulation fidelity, allowing Toyota to program and optimize complex robotic hot forging routines in realistic simulations, the companies said.
One of the key advantages of this collaboration is the “sim-to-real” workflow, where programs proven in a simulated environment can be transferred seamlessly into live production work cells. This eliminates the need for programming in the physical installation, reducing safety concerns around hot parts. ForgeOS controls both the simulation and physical work cell, enabling quick program transfers and updates, minimizing downtime and simplifying maintenance.
An innovative aspect of this workflow is ForgeOS’ capability to relay real-time production data from the live cell back to the original Nvidia Isaac Sim simulation. This creates a digital twin of the live cell, allowing for visualizations of its current state and enhancing monitoring and oversight.
Kel Guerin, chief innovation officer at Ready Robotics, said in a statement, “Nvidia provides the tools needed to help our programs reflect real-world situations, and ForgeOS provides the connection from this simulation to the real cell and back.”
Ready Robotics is collaborating with SCSK, a leading Japanese IT services company and Nvidia Omniverse partner, to bring this solution to Toyota.
Kazuhiro Suzuki, group manager of Toyota’s raw materials development division, said in a statement, “The unique architecture of ForgeOS allows for the sim-to-real workflow we need for this production line because it bridges Nvidia Isaac Sim’s simulation capabilities with the control of our physical system. This means we can program in simulation, transfer that program, and then use ForgeOS to capture live production data and iteratively improve our processes.”
Toyota’s collaboration with Ready Robotics and Nvidia signifies a significant advancement in robotic automation programming, promising greater efficiency, usability, and safety. The initiative also opens avenues for capturing production data from automation systems for use in process monitoring, improvement, and potential applications in artificial intelligence.
Deepu Talla, vice president of embedded and edge computing at Nvidia, said in a statement, “Simulating industrial processes in high fidelity prior to their real-world deployment can greatly improve productivity and safety while reducing costs.”
Toyota partnered with Ready Robotics to simulate and program industrial robotics using Nvidia’s Omniverse platform.
The “sim-to-real” robotic programming aims to advance industrial robotics, using both Ready Robotics’ Ready ForgeOS and Nvidia Isaac Sim on the Omniverse platform. Toyota will use the tech for its aluminum hot forging production lines.
The tech is the latest expression of digital twins, where a company simulates a factory in a virtual space, perfects the design, and then builds the factory. The factory, augmented with sensors, sends data back to the digital twin so that the design can be improved based on real-world data. Nvidia’s Omniverse is a platform for digital twins and it’s akin to a metaverse for engineers.
The collaboration is designed to elevate safety and efficiency in Toyota’s manufacturing processes. Traditionally, programming robotic systems for forging involves working with hot metal parts, posing significant safety challenges. The integration of ForgeOS and Nvidia Isaac Sim enables seamless programming in a simulated environment, eliminating risks associated with hot parts.
Ready Robotics simplifies the programming process for robotic systems with ForgeOS, offering time-saving automation solutions. The integration of ForgeOS with Nvidia Isaac Sim ensures best-in-class visual and physics-simulation fidelity, allowing Toyota to program and optimize complex robotic hot forging routines in realistic simulations, the companies said.
One of the key advantages of this collaboration is the “sim-to-real” workflow, where programs proven in a simulated environment can be transferred seamlessly into live production work cells. This eliminates the need for programming in the physical installation, reducing safety concerns around hot parts. ForgeOS controls both the simulation and physical work cell, enabling quick program transfers and updates, minimizing downtime and simplifying maintenance.
An innovative aspect of this workflow is ForgeOS’ capability to relay real-time production data from the live cell back to the original Nvidia Isaac Sim simulation. This creates a digital twin of the live cell, allowing for visualizations of its current state and enhancing monitoring and oversight.
Kel Guerin, chief innovation officer at Ready Robotics, said in a statement, “Nvidia provides the tools needed to help our programs reflect real-world situations, and ForgeOS provides the connection from this simulation to the real cell and back.”
Ready Robotics is collaborating with SCSK, a leading Japanese IT services company and Nvidia Omniverse partner, to bring this solution to Toyota.
Kazuhiro Suzuki, group manager of Toyota’s raw materials development division, said in a statement, “The unique architecture of ForgeOS allows for the sim-to-real workflow we need for this production line because it bridges Nvidia Isaac Sim’s simulation capabilities with the control of our physical system. This means we can program in simulation, transfer that program, and then use ForgeOS to capture live production data and iteratively improve our processes.”
Toyota’s collaboration with Ready Robotics and Nvidia signifies a significant advancement in robotic automation programming, promising greater efficiency, usability, and safety. The initiative also opens avenues for capturing production data from automation systems for use in process monitoring, improvement, and potential applications in artificial intelligence.
Deepu Talla, vice president of embedded and edge computing at Nvidia, said in a statement, “Simulating industrial processes in high fidelity prior to their real-world deployment can greatly improve productivity and safety while reducing costs.”
VentureBeat’s mission is to be a digital town square for technical decision-makers to gain knowledge about transformative enterprise technology and transact. Discover our Briefings.
Author: Dean Takahashi
Source: Venturebeat
Reviewed By: Editorial Team