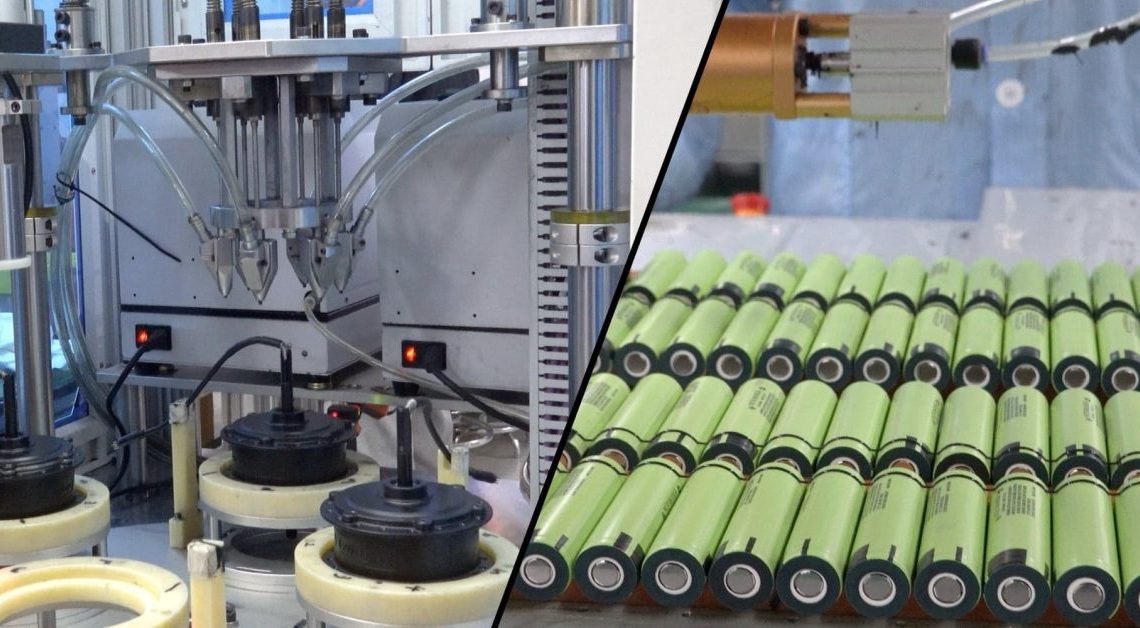
If you’ve been hanging around in the world of electric bikes for any decent amount of time, you’ve probably come across Bafang. They don’t make electric bikes, but they’ve long made many of the components used by them. I visited the factory back in 2019, and recently returned for a second visit to see what had changed. Boy, was I unprepared for what awaited me.
When I say that Bafang makes many of the components found in the e-bike you probably have at home, that now seems like an understatement. With all of the new tech and developments the company has made, they now produce just about every part used in electric bike drive systems.
And not only that, but their production processes have changed significantly over the last few years.
To see behind the scenes yourself, check out my video from the visit below.
Even from the first moment I walked through the gates, the updates were apparent. Since my last visit, Bafang has moved into a massive new complex, which is important since some of their new production now includes the addition of full e-bike battery design and manufacturing. That obviously requires significantly more of a footprint than just a motor and drive system maker.
But before I get to the new battery work, let’s start at the beginning. I began my visit in the R&D department, where a dedicated team of engineers and designers work together on drawing up the next generation of e-bike components. When I visited in 2019, there were hints in the air that Bafang was working on a solution to the common issue of e-bike motors having an unfortunate tendency to wreak havoc on traditional bicycle transmissions. There’s just a limited amount of power that most bicycle shifters and derailleurs are designed for, and that amount usually falls above leg power but below motor power.
Now I was pleased to see that Bafang has several options for their own in-house developed transmissions built around internally geared hubs (IGHs). IGHs are prized in the bicycle world for their clean, low-maintenance design that completely replaces a hanging derailleur. However, the use of an internally geared hub generally means you can’t use a hub motor (or have to put it in the front wheel, which is less desirable). But not only has Bafang developed their own IGHs, but they’ve even incorporated hub motors into the design, creating multi-speed transmissions that share the same wheel hub as an electric motor. That innovation, known as the Bafang GVT line (Gear Variable Transmission), opens a whole new world of e-bike possibilities by putting an internally geared hub and a hub motor in the same product. And on top of that, the shifting occurs entirely automatically and without external cables or wires. Clever use of mechanical components keeps the entire thing sealed and without additional external components that can wear out or fail.
I was able to check out a few of these designs in Bafang’s showroom, and even tested them out later in the day on a few different e-bikes sporting Bafang’s components. But alas, I’m getting ahead of myself.

A big part of R&D goes beyond just imagining new components. Bafang has to rigorously test their designs to ensure they can handle the harsh world in which e-bikes live. From pressure tanks of water that expose any air gaps in motors to brutal drop tests and shaker tables, the company’s engineers absolutely torture these poor devices while looking for how and where they can fail.
That testing not only leads to design improvements, but sometimes even to the development of new materials. Bafang uses their own proprietary material for the gears used in their motors, offering more strength and ruggedness than typical nylon gears, but less noise than steel gears.
There are soundproof rooms for making the most minute measurements of the sounds produced by various components, and even an EMC (electromagnetic compatibility) chamber for electrical safety testing and compliance certification, where e-bikes and components can be tested to ensure that all of the various pieces are working together properly without creating any unnecessary or potentially problematic electromagnetic radiation. This is also critical to ensuring compatability of various electrical components so that they don’t interfere with one another.
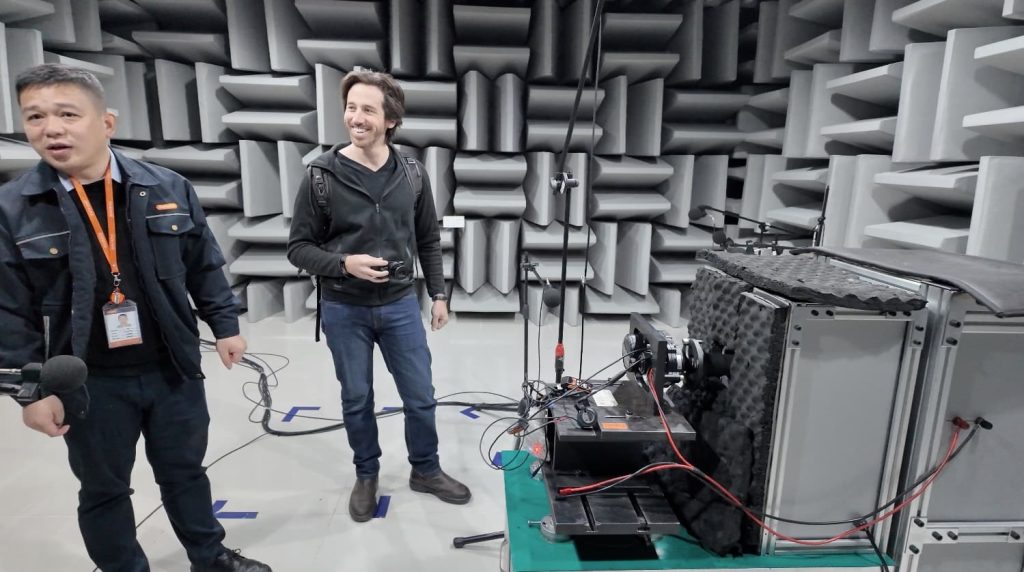
With a better understanding of the process that goes into R&D, I moved on to the factory where production occurs. Here it all begins in with quality inspections that ensure that the components that go into Bafang’s products are within manufacturing tolerances. Components like motor shells and bearings are critical to the performance of an e-bike’s drive system, and so components are scrutinized in fine detail with micron-level measurements before they make it to the factory floor where they will be incorporated into assemblies.
After passing their checks, components head into a largely automated process. For example, the motor shells are handled by robots that move them through several stages on an assembly line, adding gears, spreading grease, and receiving their motor cores.
Those motor cores pass through their own robotic lines, with the copper wire spun by precision machines. This type of work was often done by hand years ago, but has now been supplanted by automated machines that are faster and more accurate.
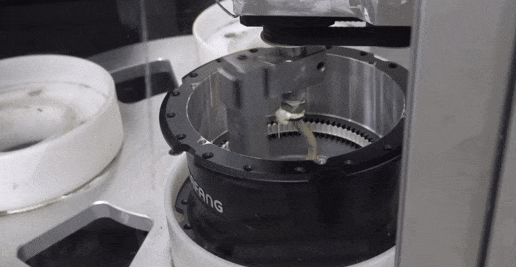
At this point, the sub-assemblies move to a final assembly line, one of the few places you still see a large number of human workers. Here, mid-drive motors receive their final assembly by hand. There are still several differences I noticed though, such as the lack of laser-engraved serial numbers, which have now been replaced by special stickers that retain the motor shell’s corrosion-resistant finish instead of engraving it away. The single sticker also replaces the several stickers of various sizes and shapes that use to offer a hodgepodge of information, and have now been streamlined into a single unobstrusive marker that also leaves the protective coating of the motor’s shell unaffected.
Motors are tested one final time on a bench apparatus, ensuring they meet all the correct specifications, before reaching their final stop on the conveyor belt: packaging.
Nearby, another machine sorts small parts such as nuts and washers that are included with products like hub motors, automatically bagging them to be included in the motor boxes.
It’s a similar story for several other components I saw, from handlebar displays to wiring harnesses. Much of the process has now been automated with special machines that automatically strip wires, mount connectors, glue display covers, and other steps that are highly manual and repetitive. Not everything has been replaced by robots, and you certainly still see many line workers, but a significant number of the tasks have been automated, and that seems like a trend that will continue.

One other intersting update I saw was a change to the way the soldering stations are set up. Previously, fumehoods were mounted above soldering stations that would suck out the fumes from the soldering operations.
That helps prevent those fumes from building up in the room, but the individual workers at each booth aren’t as protected since the fumes still pass by their faces.
The new setup has vacuum holes in the actual workstation surface that suck the fumes down and out through the table, preventing even the initial worker from being exposed to soldering fumes.
It’s a nicer setup that protects everyone, and I was glad to see the upgrades.

Bafang Battery Factory
The next part of the tour took me into the battery factory, which was like entering a brave new world for an e-bike parts supplier. Generally, battery factories are standalone operations run purely by battery makers. But Bafang has grown so large that at this point, it makes sense for them to invest in building their own high quality battery packs. It’s something they’ve been studying for nearly a decade, mostly staying in the R&D phase. But in the last few years, they’ve brought those designs to life and entered full battery production.
Again though, I’m getting ahead of myself. Becuase it’s that design stage that is critical to the quality and safety of batteries. Similarly to the e-bike drive system side of things, the battery factory has its own R&D section that scrutinizes different cells and batteries while preparing and testing new designs to ensure they can meet the proper safety and performance requirements set by Bafang. Assuming they do, they may end up slated for production and become one of the company’s new battery pack offerings.
Production on the factory floor starts with the individual battery cells that will eventually make up the larger battery packs. They are tested to ensure they pass quality checks before being automatically sorted by robots into the most appropriate combinations of cells based on similar internal resistances.
Computer-controlled ultrasonic welding machines then combine those battery cells into larger packs, which are encased in various enclosures depending on the specific model of battery. Before the battery cases are even sealed, each battery is put through a series of bench tests to ensure it meets the proper parameters. After the batteries pass those checks, they get sealed and sent to perform a complete testing cycle, where rows of shelves house hundreds – maybe thousands – of actively charging and discharging battery packs. After getting the green light following a successful charge and discharge cycle test, the battery is finally packaged and prepared to be sent on its way to an e-bike factory.
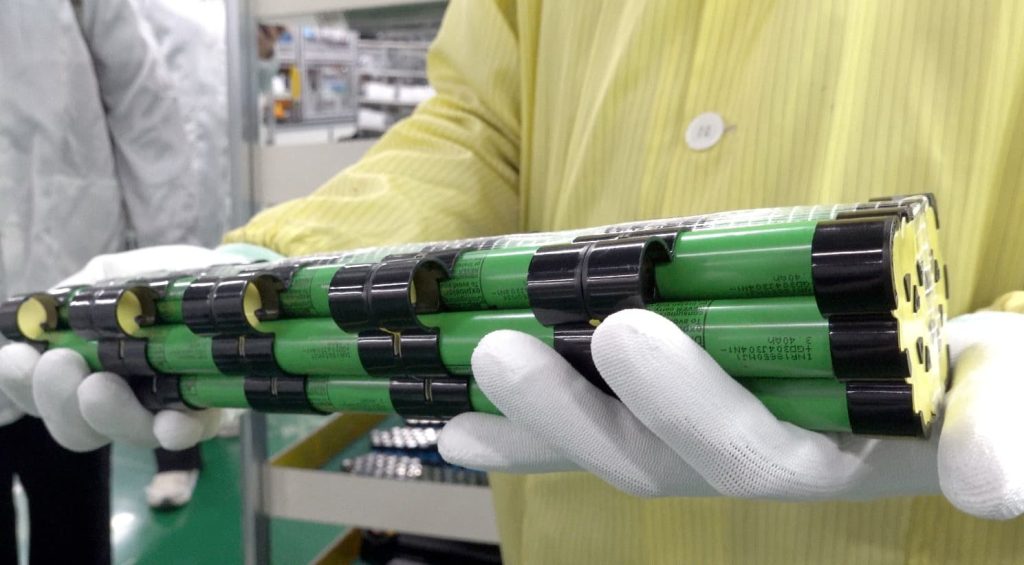


The scale of Bafang’s operations is nothing short of impressive. I’ve visited dozens of Chinese factories at this point but I’ve never seen such an all-encompassing operation from an e-bike component maker. With the addition of battery packs, not to mention all the other drivetrain components made by Bafang, the company truly is a one-stop shop now for e-bike OEMs.
It has been an incredible experience to see not just the components and designs, but the way that production has fundamentally changed inside of Bafang’s walls over the last several years. And at this rate, I’m fascinated to see what new innovations the next few years may bring.
Don’t forget to check out the video of this behind-the-scenes tour, below!
Author: Micah Toll
Source: Electrek