
I was invited to tour Bosch’s Charleston, South Carolina, facility to see firsthand the evolution of the world’s largest auto parts supplier as the industry transitions to electric vehicles.
Stepping into the facility is like entering Willy Wonka’s chocolate factory, but instead of chocolate rivers and little orange people, it’s filled with highly trained, motivated workers and next-generation technology working together in sync.
The company uses industry 4.0 production methods featuring artificial intelligence, precision lasers, robotics, and more to build precise, reliable auto parts at scale.
Bosch’s Charleston facility makes critical components for the auto industry shipping them out to nearly every major automaker, including Tesla, Ford, GM, and one of its latest customers, Rivian.
However, as the President of Bosch in North America, Mike Mansuetti, explains, the auto industry is “rapidly evolving” toward electric vehicles. The auto parts supplier is investing in a sustainable future by introducing new EV products and parts for its customers, bringing the technology to market at scale.
Mr. Manuetti says:
We’ve invested more than $6 billion dollars in electromobility development and
in 2021 our global orders for electromobility surpassed $10 billion dollars for the
first time. Local production helps to advance our customers’ regional
electrification strategies, and further supports the market demand for
electrification.
Bosch announced in January 2020 that it would begin to slow production of its diesel powertrain components to focus on sustainable solutions. A prime example of the rapidly evolving industry, the building is now being used to build electric motors for the Rivian R1T.
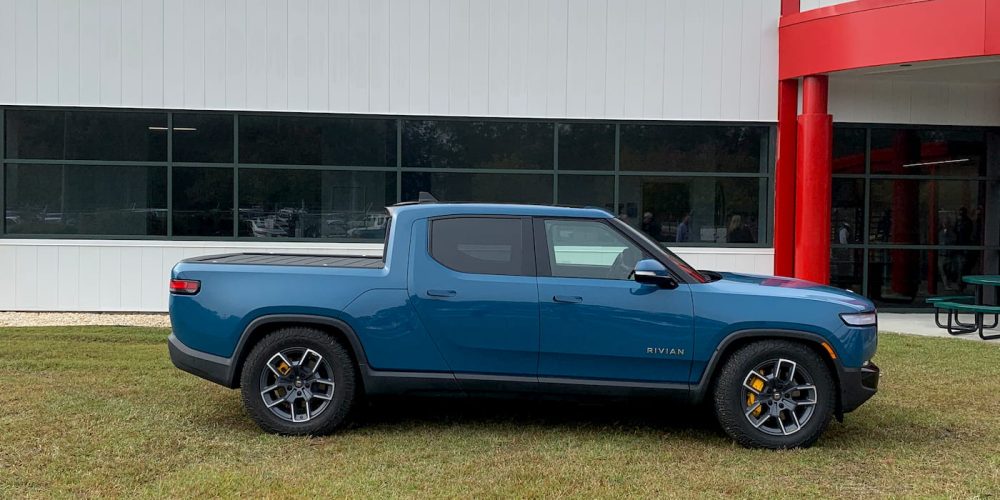
Bosch is building its portfolio to power electric vehicles
Bosch began production of the electric motors in October for the Rivian R1T, marking a “new era of electrification” for the global auto parts leader. The manufacturing site covers around 200,000 square feet in the previously used diesel components area.
The electric motor consists of two primary parts – the rotor and the stator. The stator features winded copper bars for superior efficiency and power density. The coils receive energy from alternating current coming via power electronics from the battery.
Meanwhile, the rotor is filled with magnets by the process of transfer molding to promote fewer air pockets. As the current flows into the stator, the rotor’s magnetic field chases that of the stator, generating energy that powers the vehicle’s wheels. The casing then consists of an aluminum A-shed and B-shed that enclose the unit.
The company utilizes high-tech AI-powered machinery and other robotics to reduce its carbon footprint while producing faster, more accurate results.
According to Bosch, its electric motor features 98% efficiency. In addition, the process is scalable, allowing more freedom to customers, delivering anywhere from 50 kW up to 500 kW with a torque range from 150 Nm to 1000 Nm and up to 680 HP.
Since electric vehicle motors differ in size, scope, and material, the new production process came with challenges. Perhaps, more importantly, the shift to electric vehicles is creating a gap in workers to fill these high-tech manufacturing jobs.
Realizing this, Bosch is providing reskilling and upskilling opportunities for its employees while partnering with local schools to ensure there is the talent needed to propel the future of the auto industry.
Investing in electromobility training
As Bosch explained, the transition would not be possible without the workers. To accelerate the process, employees were sent to Bosch’s plants in Germany for training and to learn how they could make the manufacturing process more efficient with automation.
As a result, these are not your typical manufacturing jobs. These are high-tech jobs that involve skills such as software programming and working with automated machines.
If you think about it, when you bring your car in for a checkup, it’s not a toolbox the mechanic brings out anymore. It’s often a laptop designed to pinpoint the issue automatically. Electric vehicles are more sophisticated and therefore require a different skill set to work on.
Vehicle suppliers play an integral role in the US economy, contributing to around 2.5% of GDP. As electric vehicles continue gaining momentum, surpassing gas-powered vehicle sales, the workforce will need to be able to support the transition.
Bosch’s $260 million expansion is expected to create 350 net new jobs by 2025, and this is just the start. To position itself for the future in the auto industry, Bosch is partnering with local schools in Charleston, such as Trident Technical College, to integrate electric vehicle education into the curriculum.
The auto supplier’s corporate foundation, The Bosch Community Fund, has provided $2.5 million in STEM education efforts in the Charleston area since 2013.
Electrek’s Take
With electric vehicles on track to claim 13% of global new car sales in 2022, the rapidly evolving auto industry is establishing a new stream of jobs. What Bosch is doing is taking employees that were previously working on parts for gas-powered cars and training them for the future of the industry.
However, the company is finding that there are major stigmatizations and built-in perceptions around manufacturing jobs that don’t apply anymore.
People will not be interested in what they don’t know. These manufacturing jobs utilize skills that some kids use essentially every day, like video games that require quick thinking and analytical skills.
The issue is that educators are unaware of what future manufacturing jobs will look like, thanks to the electric vehicle revolution. Teachers are not pushing for these jobs because they don’t associate them with the skills that they will be using. Same idea with parents.
To support the new EV era, what needs to happen is a change in perception that gets people interested in the auto industry’s future and putting the US back on track to become a manufacturing powerhouse.
Last year, new electric vehicle jobs soared 26.2%, establishing 21,961 new positions. And this year, the pace has accelerated even further with new climate initiatives and substantial investments from foreign automakers on US soil.
Since the beginning of 2021, companies have invested around $85 billion in manufacturing operations for electric vehicles, batteries, and chargers, all of which require a new set of skilled workers.
The opportunities electric vehicles are creating in the United States are already showing, and the EV market share is just reaching 6%. Imagine what will happen in another year.
Bosch, the largest auto supplier worldwide, will play a significant role in the transformation. During my visit, they seemed eager and up to the challenge of supporting the incoming wave of electric vehicles and the future of the industry.
Subscribe to Electrek on YouTube for exclusive videos and subscribe to the podcast.
Author: Peter Johnson
Source: Electrek